Mazda's efforts in Group-A rallying began in 1986 with the homologation of the previous-generation 323 4WD powered by the turbocharged 1,623-cc DOHC engine. The works sponsored team scored outright victories in the 1987 Swedish. 1989 Swedish and 1989 New Zealand rallies. In 1989, Mazda launched the 323 4WD GTX model, from which a new championship Group-A car was derived, powered by the new type BPD 1,839-cc DOHC, 16-valve turbocharged engine. The Group-A GTX made its debut in the 1990 Rally of Thousand Lakes, in which it placed 6th overall. Mazda continued to campaign the GTX through 1991 and into the 1992 season, until the homologation and debut of the GT-R based car powered by the "Big Turbo" DOHC 1,839-cc unit. At that time the regulations governing International Group-A rallying as implemented by FISA were being further tightened. The changes included a smaller air-intake restrictor (from 40mm to 38mm effective 1992), a minimum kerb weight of 1,200 kg (for the 1.8-2.0 litre class), and a maximum gravel tyre diameter of 650mm, and a maximum tarmac wheel rim width down to 9-in. (the kerb weight, tyre diameter and wheel rim width changes coming into effect in 1993) The 323 4WD GT-R was designed and developed with these regulatory considerations in mind, and was expected to be extremely competitive as soon as it was homologated. The Group-N category was another important rally arena. With the 323 4WD, private entrants won the 1988 and 1991 World Driver's Championships and the 1989 Manufacturers Championship for Mazda. 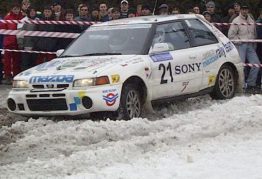 Group A competition regulations prohibit modification of certain engine components. The GT-R design team have included the following performance boosting parts and modifications in the stock engine. The GT-R's turbo-charger exhaust and compressor rotors have been increased from 52.5mm to 62mm and the A/R ration has risen from 15 to 16. The design team selected these specifications after thorough testing, in line with the basic engineering policy of maximizing boost pressure at the top end, while minimizing turbo-lag. Low-friction ball bearings replace the GTX,s floating-metal bearings in the water-cooled turbo-charger journal. Components are made from new heat-resistant materials to withstand rigorous rally conditions 1 A new larger-diameter duty valve at the waste gate is under microcomputer control. The same microcomputer regulates the intercept point and maximum boost pressure settings The intercooler core size is 70% larger, up from 125mm x 247mm in the GTX, to 225mm x 234.6mm for the GT-R. Performance has soared 37% from 4.500 kcal/h to 6.150 kcal/h. The cooling fins are arranged in zigzag pattern which increases cooling efficiency. The intercooler is mounted in front of the radiator to catch the cool air stream, lowering the intake gas temperature to prevent engine knocking, The intercooler's square shape and tube layout minimizes pressure loss. 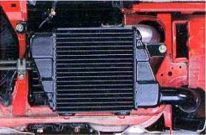 |
The surge tank wall baffles equalize intake air pressure, reducing cylinder overload and improving performance and reliability. This design was pioneer by Mazda engineers and developed following extensive testing. The technology is a world first and Mazda holds the patent The exhaust manifold is made of lightweight, heat resistant ferrite steel. Lost-foam casting gives the manifold its smooth inner surface which reduce gas flow resistance. The con-rods are made of a tougher alloy and their "I"-shaped cross-sections provide rigidity and strength. The stock GT-R engine contains numerous modified parts over the GTX that increase the car's potential for Group N competition. The capacity of the air flow meter, fuel pump, and fuel injection system have increased for higher power output. The exhaust valve stems are hollow and partially filled with sodium. As the valves heat up, the sodium melts and is agitated violently as the valves move. Heat is absorbed from the valve neck by the liquid metal and conducted to the valve stem where it dissipates. The cooler exhaust valves prevent predetonation, increasing engine reliability. The forged aluminum pistons with cooling channels, resemble Formula One engine pistons. The piston crowns are tin plated. There are two compression rings and one oil ring. Nickel cement is fuse-bonded to the groove area of the top ring to enhance wear resistance. The well-lubricated kelmet metal con-rod big-end bearings are the same as those fitted in Group A competition motors. The new five-stage water-cooled oil cooler has a greater capacity over the GTX's old two-stage unit. Oil jets spray oil up into the cooling channels in the underside of the pistons, cooling the piston crowns Exhaust temperature and pressure is reduced by minimizing the number of cells in the catalytic converter and by straightening the silencer's internal construction.
|